Summary
Find What You Need
Browse our range of Fall Protection to find the perfect solution for your needs.
The Lifespan of Fall Protection Equipment
Ensuring worker safety heavily relies on understanding the lifespan of fall protection equipment. The Occupational Safety and Health Administration (OSHA) provides critical guidelines aimed at the effective management of personal protective gear. These insights are pivotal in maintaining a safe and compliant work environment. OSHA Fall Protection Standards offer essential regulatory information.
Typical Lifespans for Equipment
Standard fall protection equipment, including safety harnesses and lanyards, typically boasts a serviceable life ranging from three to five years. However, this timeframe is not an unyielding rule. Specific conditions may necessitate a sooner replacement. Manufacturers often delineate suggested service durations within their documentation, urging users to adhere to such guidelines for optimal safety.
Factors Influencing Service Life
Various elements can affect the longevity of safety harnesses and associated equipment. Recognizing these influences aids in informed decision-making concerning equipment retirement:
Frequency of Use: Increased usage accelerates wear and tear, leading to a shortened service span.
Environmental Exposure: Harsh conditions such as extreme temperatures, consistent moisture, or chemical contact expedite deterioration.
Storage Conditions: Storing gear in cool, dry environments significantly bolsters longevity.
Maintenance and Inspection: Routine assessments and diligent maintenance can stave off premature degradation.
Compliance with Standards: By adhering to relevant regulations, equipment maintains its protective capabilities and avoids undue wear.
Understanding Equipment Expiry
The question of whether fall protection gear expires is common. These items lack an explicit expiration date, instead reflecting a suggested replacement window. Over extended periods, materials like nylon and polyester experience weakening, particularly under adverse conditions.
Frequent inspections hold paramount importance. Comprehensive evaluations help identify damage—such as diminished tensile strength or visual deficiencies—that renders gear unsuitable. OSHA protocols underscore routine appraisals to swiftly address potential safety risks.
Safety Harness Considerations
Safety harnesses, in particular, demand meticulous scrutiny. Steps for examining harnesses include:
Checking for frayed straps or cuts
Evaluating stitching integrity
Inspecting hardware for defects, such as compromised buckles or D-rings
Noticing any deficiencies signifies the need for replacement, regardless of the harness's age. Accurate documentation during these inspections enhances workplace accountability and fortifies the overarching safety culture.
Recognized as industry leaders
Our awards highlight our commitment to innovation, quality, and delivering exceptional results.
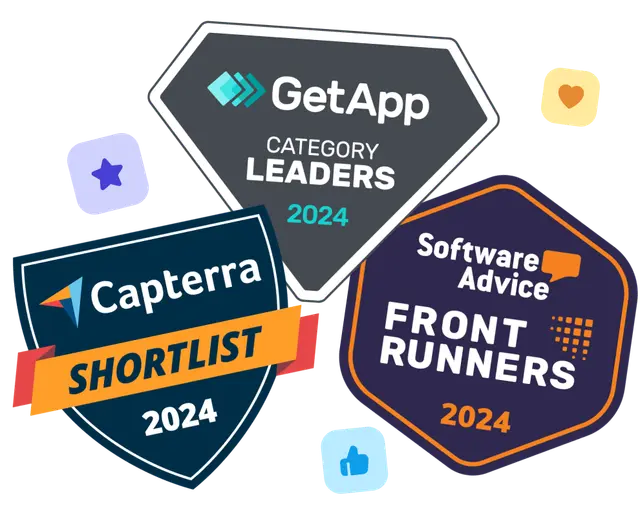
Maximizing Equipment Lifespan
Employing best practices effectively extends fall protection equipment lifespan:
Regular Inspections: Enforce frequent gear examinations, ideally before every use.
Training Personnel: Educate personnel on proper fitting, adjustment, and wearing techniques.
Establishing Guidelines: Implement comprehensive policies surrounding maintenance, inspections, usage, and storage.
To maintain rigorous safety standards, businesses must prioritize detailed fall protection programs aligning with OSHA regulations. Organizations willing to invest in thorough upkeep and continual evaluations guarantee long-lasting reliability, mitigating risks associated with malfunctioning or outdated equipment.
Ultimately, a proactive approach towards equipment care not only safeguards personnel but also embodies a commitment to safety excellence. By understanding and applying the factors that influence equipment lifespan, businesses can ensure their gear remains in optimal condition, thus providing robust protection in environments where safety cannot be compromised.
Inspection and Maintenance of Safety Harnesses
Safety harnesses play a crucial role in fall protection systems, providing security for workers at heights. Regular inspection and maintenance remain paramount in ensuring these devices' effectiveness and longevity. Ignoring this critical aspect can lead to potential failures and increased risk of injuries.
Importance of Inspection
Thorough inspection is vital in detecting wear, tear, and other defects before they compromise user safety. According to the CDC Workplace Safety & Health Topics, regular checks are necessary. The integrity of harnesses ensures life-saving capabilities during a fall event. Inspections focusing on hardware, webbing, stitching, and attachments take a comprehensive approach that uncovers hidden problems promptly.
Steps in Conducting Inspections
Visual Examination: Begin with inspecting the harness for frayed or cut webbing, missing labels, and any discoloration. Identifying these visual cues can often indicate structural damage lurking beneath the surface.
Testing Stitch Integrity: The need to check all stitches for intactness cannot be understated. Any unraveling suggests compromised strength, demanding the harness's immediate retirement to avert potential dangers.
Checking for Rust and Deformation: Metal components require scrutiny for signs of rust, corrosion, or deformation that weaken the harness's capacity to bear loads. Ensuring rust-free, well-shaped metal parts guarantees harness reliability.
Functionality of Buckles and D-rings: Every inspection should include testing the buckles and D-rings for proper locking mechanisms. Wear from use is not uncommon and should be addressed to maintain reliability in demanding situations.
Conduct inspections at least bi-annually, or more frequently in rigorous work environments, maintaining unrivaled safety standards.
Maintenance Practices
Maintenance goes hand-in-hand with inspections, prolonging the safe use of harnesses. Initiating regular maintenance routines ensures minor issues can be rectified, preventing significant failures in future usage. Proper storage is integral; harnesses need to remain dry and shielded from UV rays to prevent premature material degradation. Cleanliness maintains equipment integrity, removing harmful substances that may latch onto harnesses during use, potentially compromising their safety and function.
Speak to an expert
Talk to our team about your safety or procurement needs. We’re here to help you find the right solution.
Contact UsLifespan of a Fall Protection Harness
Several factors determine a safety harness's lifespan, including frequency of use, exposure to harsh environments, and adherence to maintenance protocols. Although manufacturers provide specific guidelines, many advocate for replacement every 2 to 5 years. Despite this range, damage discovered through inspection may necessitate earlier retirement.
Ensuring Worker Safety and Compliance
Regular inspection and effective maintenance of safety harnesses bolster worker security while ensuring compliance with occupational safety regulations. Organizations must instill a proactive approach, with workplace leaders emphasizing the value of these essential habits among their teams. Conducting training sessions highlights best practices and raises awareness about fall protection equipment care and management. For more comprehensive guidelines, consider visiting the CDC Workplace Safety & Health Topics resource page.
Rigorous inspection and maintenance of safety harnesses are indispensable parts of a safety management system. Adhering to these practices guards against equipment failure and introduces a safer working environment for professionals operating at heights. Protecting lives and fortifying regulatory compliance remains a top priority for ensuring a successful operation.
Frequently Asked Questions
What is the expiry date for a safety harness?
Safety harnesses play a crucial role in the efficacy of fall protection systems. Manufacturers usually set a defined lifespan for these harnesses, typically recommending replacement every five years. This timeframe varies depending on multiple variables, including environmental conditions, frequency of use, and adherence to inspection protocols. The Occupational Safety and Health Administration (OSHA) stresses the importance of regular inspections before each use. These inspections help ascertain a harness's integrity, ensuring users' safety. For specific guidance on expiration, maintenance, and compliance, always consult the manufacturer's instructions OSHA Fall Protection FAQs.
What factors influence the lifespan of fall protection equipment?
The longevity of fall protection equipment is influenced by numerous elements, such as harsh environmental exposure, physical damage, frequency of utilization, and proper storage practices. Ultraviolet (UV) light exposure, excessive heat, weathering, and contact with chemicals can deteriorate materials used in harnesses and lanyards. To counteract these effects, implement stringent inspection routines and follow manufacturer guidelines to optimize equipment lifespan. These preventive measures ensure that equipment remains robust and reliable for users across various work environments.
How do you determine if fall protection equipment needs replacement?
Determining the need for replacement involves a thorough inspection of equipment for any signs of wear, damage, or failure. Key indicators prompting replacement include frayed webbing, missing or unreadable labels, cracks in metal components, and compromised stitching. Manufacturers provide detailed checklists to aid inspectors in evaluating equipment condition. Regular inspections before each use, coupled with comprehensive annual assessments, ensure that protection and compliance are maintained across different operational settings.
What are the most common types of fall protection equipment?
Fall protection systems comprise a range of equipment, each designed for specific safety functions. Common types include full-body harnesses, lanyards, energy absorbers, self-retracting lifelines, and anchor points. Full-body harnesses offer secure attachment, lanyards connect users to anchor points, and self-retracting lifelines provide necessary mobility. Selecting and using the appropriate components is crucial for ensuring optimal safety across diverse workplace environments, addressing unique challenges and requirements.
Why is proper training crucial for using fall protection systems?
Proper training forms the backbone of safely utilizing fall protection systems. It ensures that users understand equipment usage, aligning with industry standards and regulatory demands. Lacking adequate knowledge can lead to misuse, increasing accident risks significantly. Employers have an obligation to offer comprehensive training programs, covering equipment inspection, correct fitting, and practical usage techniques. These training initiatives bridge knowledge gaps, enhancing the overall occupational safety framework.
How does expiry impact the performance of fall protection equipment?
An expired fall protection component does not indicate immediate failure but signals reduced assurance in its performance. Past this point, materials may potentially degrade, impacting resilience and functionality. Monitoring through regular inspections and adhering to replacement schedules is critical in maintaining the integrity and effectiveness of fall protection systems. This proactive approach safeguards users, ensuring workplace safety remains the priority.
For further insights and guidance, resources from entities like OSHA offer comprehensive guidelines, aiming to fortify safety protocols in the workplace. Leveraging these resources can elevate safety measures, aligning operations with best practices for enhanced protection and compliance.