Summary
Find What You Need
Browse our range of Fall Protection to find the perfect solution for your needs.
Fall Protection Harness Expiration: Understanding the Essentials
Safety professionals often grapple with determining whether fall protection harnesses expire alongside establishing an effective timeline for replacement. These harnesses serve a crucial role in protecting employees from potential falls. Through careful consideration of relevant factors and standards, it becomes possible to ensure maximum protection for workers in high-risk environments.
Grasping Lifespan Assessment
Surprisingly, specific expiration dates for fall protection harnesses are not defined by standard guidelines. Authorities like OSHA, while offering extensive standards on fall protection, do not pinpoint an exact expiration. Industry experts and leading manufacturers, however, stress the necessity of regularly assessing these safety devices based on condition, usage history, and manufacturer instructions.
Key Factors Influencing Harness Expiration
Critical elements determining harness lifespan include:
Material Quality and Durability: Superior materials and sturdy construction typically promise increased longevity. Conversely, lackluster materials tend to degrade more rapidly.
Usage Frequency: Regular use inevitably leads to faster wear and tear, lessening overall lifespan.
Environmental Exposure: Harsh conditions, such as extreme temperatures, UV exposure, chemicals, and moisture, can expedite material breakdown.
Storage Protocols: Proper storage away from detrimental conditions substantially extends a harness's life expectancy.
Heeding Manufacturer Guidelines
Each harness comes with manufacturer-supplied guidelines highlighting an expected lifespan—usually spanning 3 to 5 years—subject to product and conditions. Adhering strictly to these recommendations is essential for maintaining safety standards and ensuring worker protection.
Routine Inspections: A Safety Imperative
Regular inspections stand as critical endeavors in spotting wear, damage, or degradation:
Watch for frayed or abraded straps.
Be vigilant for broken stitches.
Look for distorted metal components.
Ensure malfunctioning buckles are addressed.
These checks conducted by trained inspectors before use and formal annual assessments play a pivotal role in keeping equipment safely operational. Identifying the end of a harness’s functional safety necessitates these thorough inspections.
Formulating a Replacement Plan
Though fall protection harnesses lack a fixed expiration, devising a proactive replacement plan is paramount. Reliance on regulatory guidelines, alongside manufacturer recommendations, advances safety ambitions while fostering informed budgetary planning for future acquisitions.
Incorporating these considerations into operational strategies enables effective management of fall protection harness life cycles, reinforcing safety measures and promoting regulatory adherence. A structured approach to lifecycle management safeguards the well-being of valuable workers and mitigates potential compliance risks across various industry sectors.
Importance of Regular Inspection and Maintenance in Fall Protection
Ensuring the safety and long-lasting use of fall protection harnesses is critical. Regular inspections and maintenance are pivotal in maintaining their effectiveness. These vital procedures not only extend the lifespan of the equipment but also protect users from potential hazards.
Vital Role of Inspection
Routine inspections act as the first line of defense against equipment failure. According to the Occupational Safety and Health Administration (OSHA), fall protection equipment must undergo careful examination before every use. This involves scrutinizing harnesses for cuts, abrasions, excessive wear, or any missing components. Noteworthy damage includes breaks in webbing, torn stitching, or frayed edges. For full compliance and best practices, refer to CDC Guidelines on Fall Protection.
Effective Maintenance for Longevity
Appropriate maintenance practices keep equipment in optimal condition. After each use, harnesses require cleaning according to manufacturer recommendations. This typically includes washing with water and mild detergent, then allowing the equipment to air dry. Store these in a cool, dry location, avoiding exposure to direct sunlight or chemicals that may compromise material integrity over time.
Imperative Record Keeping
Documenting inspections serves as a cornerstone in a well-rounded maintenance program. It ensures compliance and tracks each harness's history, including use and examinations. Recording inspection dates, findings, and corrective actions can reveal usage patterns, facilitating timely replacements when necessary. This practice also promotes transparency among team members and supports future training and evaluations.
Adherence to Manufacturer's Recommendations
Every harness comes with specific recommendations from its manufacturer. Abide by these to prevent mishandling equipment. Deviation from prescribed practices can void warranties and jeopardize the harness's structural integrity. In cases of irreparable damage or wear, seek professional evaluations to determine the best course—reconditioning or replacement.
Best Practices in Harness Handling
A comprehensive approach to harness care includes frequent inspections and proactive maintenance, ensuring safety continues uninterrupted. Encourage a culture of accountability where users promptly report defects or irregularities. Regular training and staying informed about industry updates strengthen safety strategies.
Harnesses comprise a crucial component of fall protection systems, demanding consistent examination and diligent maintenance. Following established guidelines and manufacturer recommendations fosters both durability and user safety. These practices are crucial for mitigating risks and promoting secure working environments. By insisting on high standards, organizations safeguard their workforce from unforeseen accidents.
Related Products and Categories
Explore our range of Fall Protection Kits for comprehensive solutions.
Discover Harnesses tailored to various applications.
Browse Fall Protection Accessories for additional safety components.
Manufacturers' Guidelines and Recommendations
Fall protection harnesses are indispensable for ensuring the safety of workers operating at height. Understanding manufacturers' guidelines and recommendations for their proper use, maintenance, and expiration is essential in maintaining safety standards and complying with regulations.
Understanding Manufacturers' Recommendations
Manufacturers provide detailed guidelines and recommendations to guarantee the proper usage and maintenance of fall protection harnesses. These recommendations cover various elements, such as usage frequency, environmental conditions’ impact, and regular inspection routines. Adherence to these instructions ensures effectiveness throughout the lifespan of the equipment.
Importance of Adhering to Guidelines
Complying with manufacturers' recommendations significantly enhances user safety and extends the life of harnesses. Proper usage and care instructions typically involve knowledge of when to retire a harness, especially post-fall exposure or visible wear and tear. The NSC Guidelines on Fall Protection Equipment emphasize systematic inspection and adherence to manufacturers’ guidelines to prevent equipment failure and decrease risks.
Factors Influencing Harness Longevity
Several factors impact the longevity of harnesses. Material composition, exposure frequency to harsh environments, and care during use all play a role in maintaining harness safety and functionality. Understanding these elements assists safety managers in implementing an efficient equipment management system.
Inspection and Maintenance Protocols
Routine inspections are crucial for identifying potential problems before they lead to failures. Manufacturers include detailed inspection checklists and maintenance routines in their guidelines. Inspections involve looking for frayed webbing, damaged buckles, or other degradation signs. Regular preventive measures are central in ensuring harnesses remain safe and compliant with safety regulations.
Determining Expiration Dates
Expiration dates for fall protection harnesses are established by manufacturers based on material properties and expected usage. Certain harnesses come with predetermined expiration dates, while others depend on condition-based evaluations. Understanding these criteria is extensive for making informed decisions on equipment safety and lifespan.
Interpreting Maintenance Guidelines
Decoding maintenance guidelines necessitates thorough training and understanding of safety protocols. Safety personnel should engage in regular training sessions focused on interpreting manufacturers' maintenance instructions. Through training, safety professionals gain insights into optimal practices for utilizing and maintaining harness equipment.
Enhancing Safety Protocols
Manufacturers' guidelines encompass more than simple user instructions; they are vital documents shaping workplace safety protocols. Safety managers should incorporate manufacturers' recommendations into overall safety strategies. This integration ensures comprehensive protection against hazards related to falls from heights.
Accessing manufacturers' literature on equipment guidelines offers invaluable insights into optimal practices for harness usage and upkeep. Through adherence to manufacturers' instructions, safety professionals can remarkably reduce accident risks and ensure compliance with stringent safety standards.
Frequently Asked Questions
Continuously ensuring the efficacy and reliability of fall protection harnesses is vital for safety professionals across various sectors, including construction, manufacturing, and beyond. Addressed here are prevalent concerns and questions regarding the lifespan and consistent safety of these indispensable protective tools.
How Many Years is a Fall Protection Harness Good For?
Fall protection harnesses generally function effectively for five to ten years. This duration, however, is contingent upon multiple elements such as manufacturer specifications, usage conditions, and routine inspection frequency. For example, harnesses used daily in severe environments face more rapid wear, necessitating diligent inspection and possibly earlier replacement. Strict adherence to OSHA guidelines is crucial, underscoring the importance of following manufacturers' instructions to optimize safety measures.
Do Safety Harnesses Go Out of Date?
Indeed, safety harnesses possess expiration dates. Several factors, including accumulated wear and material degradation, compromise their effectiveness over time. Although years provide a general timeline, a harness's condition heavily dictates its usability. Regular physical inspections for damage, corrosion, and other signs of compromise are essential. Since manufacturer expiration policies differ, always consult specific guidelines based on materials and craftsmanship for accuracy.
What is the Shelf Life of Any Harness?
Shelf life refers to how long a harness can remain unused while still retaining its optimum safety functions. This period typically extends beyond the active usage span and often reaches around ten years if maintained appropriately. Best storage practices involve keeping the harness in a consistently dry, clean environment, shielded from direct sunlight and harmful chemicals that may induce deterioration prematurely.
Factors Impacting Longevity
Several crucial elements affect decisions about retiring a worn harness:
Material Degradation: Chemical exposure or extreme weather expedites strap material erosion. Regularly inspect for fraying, abrasions, and tears to maintain safe usage.
Connector Compatibility: Periodic evaluations of connector compatibility are necessary to ensure they adequately secure and function correctly.
Regulatory Compliance: All harnesses must adhere to OSHA and other relevant regulatory guidelines. Non-compliant equipment should be discarded, regardless of apparent visual condition.
User Wear and Tear: The inherent stress and force impact a harness endures can inflict internal harm, potentially invisible visually.
Best Practices for Managing Harness Expiration
To extend a harness's lifespan and bolster safety, adopt a comprehensive inspection and maintenance routine:
Schedule regular inspections focused on detecting visible damage or wear and tear.
Document each harness during every phase, from purchase and inspections to the projected replacement timeline.
Educate all users on proper handling, storing, and identifying defective equipment.
Familiarity with this data helps maintain adherence to safety standards within workplaces. Regularly updating safety protocols and conducting training drills reinforces the priority of harness maintenance. Seeking guidance from qualified safety professionals ensures expert insight tailored to specific circumstances, supporting continued focus on harness reliability and user protection.
Recognized as industry leaders
Our awards highlight our commitment to innovation, quality, and delivering exceptional results.
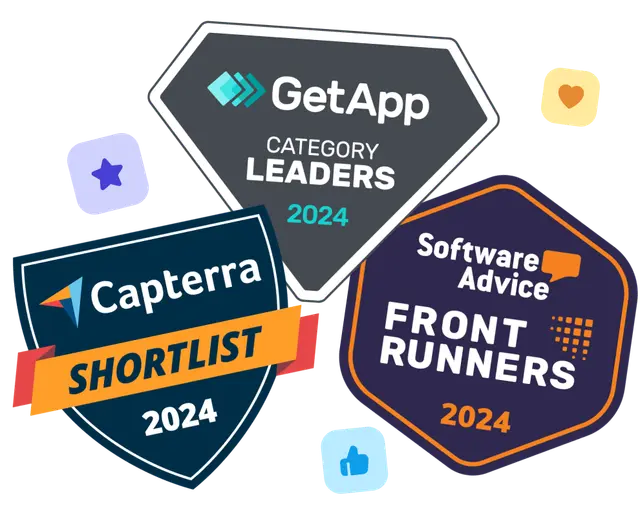