Summary
Find What You Need
Browse our range of Hearing Protection to find the perfect solution for your needs.
Introduction to Hearing Protection
Reducing exposure to hazardous sound levels proves crucial for ensuring health and safety in professional environments. Hearing protection emerges as an indispensable aspect, safeguarding individuals from long-term auditory damage due to noisy surroundings. The Occupational Safety and Health Administration (OSHA) asserts that exposure to excessive noise levels potentially results in permanent hearing loss and various other health complications.
Importance of Hearing Protection
In industrial settings, ear protection remains vital for maintaining personnel's auditory health. Utilizing earmuffs or earplugs significantly diminishes the impact of high-decibel surroundings and effectively prevents noise-induced hearing damage. This proactive measure safeguards both immediate and future well-being for workers. Without proper ear protection, workers may experience impairments in hearing, physiological stress, or even reduced cognitive function, which can negatively affect overall work performance and safety.
Contexts Requiring Hearing Protection
Certain industries necessitate rigorous use of protective gear due to their persistent elevated noise levels. Construction sites, manufacturing facilities, and aerospace operations, for example, feature machinery and processes that generate sound levels harmful to human hearing. Additionally, environments like music venues and airports usually demand hearing protection to fend off potential auditory injury resulting from prolonged exposure to loud sounds.
When noise levels reach or exceed 85 decibels (dB) over eight hours, OSHA mandates that employers implement a hearing conservation program. These programs play a vital role in educating workers about the significance of ear protection and ensure compliance with safety measures. Regular monitoring and audiometric testing provide valuable data, helping to effectively address and control workplace noise.
Best Practices and Technological Advancements
Recently, advanced hearing protection technologies have emerged, focusing on addressing diverse workplace requirements. Customized hearing protection solutions now exist, offering a tailored fit and enhanced comfort for the user. Innovations such as smart earplugs and noise-cancelling earmuffs are available, equipped with features like ambient sound amplification, Bluetooth connectivity, and automatic sound level adjustment, raising productivity and worker satisfaction.
Investing in continuous training and convenient access to proper gear fosters a culture of safety and encourages workers to prioritize auditory health. Industries must strive to implement efficient protective measures and enforce comprehensive compliance with these safeguards. A proactive approach ensures that protection measures are not only in place but adopted enthusiastically by the workforce.
Ultimately, protecting workers against detrimental sound levels contributes to a healthier, more productive workforce. To explore further details on regulations and guidelines, visit OSHA's Occupational Noise Exposure page.
OSHA Requirements for Hearing Protection
Properly safeguarding hearing in the workplace is crucial in maintaining occupational safety, particularly in sectors with heightened noise levels. The U.S. Occupational Safety and Health Administration, commonly referred to as OSHA, enforces strict regulations designed to prevent auditory injury among workers. These provisions determine both permissible noise exposure and the protective actions necessary to preserve employee well-being.
Understanding Noise Level Thresholds
Noise-induced hearing loss remains among the most common occupational hazards. OSHA standards categorize environments with noise exposure surpassing 85 decibels (dBA) over an eight-hour period as dangerous. At this point, hearing protection becomes compulsory. As noise increases, allowable exposure time decreases significantly. For instance, noise levels measured at 90 dBA permit a maximum exposure of eight hours but only four hours for 95 dBA (source).
Required Protective Measures
For workplaces that exceed the specified noise exposure limits, OSHA necessitates comprehensive hearing conservation programs. These programs incorporate several strategies, including implementing engineering controls to attenuate sound sources and supplying hearing protection devices (HPDs) to employees.
Engineering controls contribute significantly to reducing noise levels to within permissible limits. However, when these fail to achieve satisfactory results, issuing hearing protection devices (HPDs) such as earplugs or earmuffs becomes indispensable. Employees should receive devices that cater to their specific requirements and comfort, as correct fit and consistent usage are vital for optimum protection.
Hearing Protection Devices Selection
Appropriate hearing protection selection relies on understanding noise reduction ratings (NRR), which estimate the anticipated dBA reduction afforded by the device when worn properly. Technical professionals typically calculate effective noise exposure by subtracting seven from the NRR, then halving the resultant figure. As an example, a device with an NRR of 30 reduces exposure by approximately 12 dBA—rendering a 100 dBA environment essentially equivalent to 88 dBA (source).
Recognized as industry leaders
Our awards highlight our commitment to innovation, quality, and delivering exceptional results.
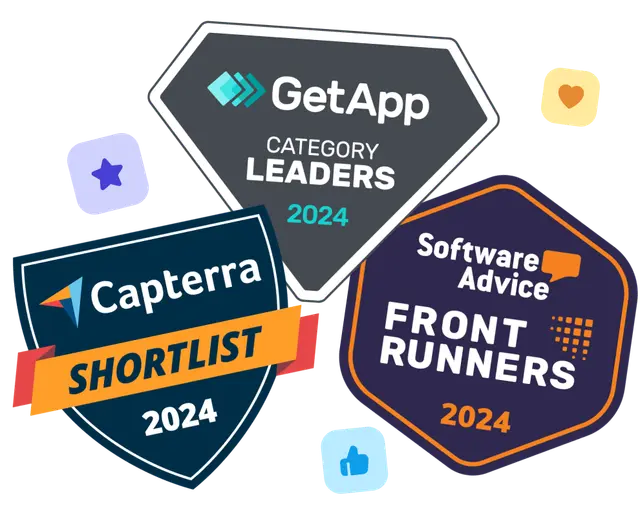
Implementation and Training
In addition to distributing HPDs, OSHA underscores the importance of employer-provided training and education for employees. Training sessions impart crucial information about the correct utilization and maintenance of hearing protection devices, their necessity, and associated risks of misuse or neglect. Educated employees who comprehend hearing risk mitigation are less prone to experiencing preventable hearing damage.
Monitoring and Compliance
OSHA compliance relies on consistent monitoring of workplace noise levels as well as routine audiometric testing of workers. These measures preemptively identify hearing loss signs and enable tailored protective solutions. Annually evaluating these practices fosters a deeper insight into noise reduction strategy efficacy customized to specific workplace conditions.
By strictly adhering to OSHA guidelines, organizations not only shield their workforce from auditory hazards but also create a safer, more productive environment that champions employees' long-term auditory health. For comprehensive information and resources, OSHA hearing protection standards can be accessed at OSHA – Ear Protection.
Types of Hearing Protection Devices
Exposure to excessive noise can lead to irreversible hearing loss, making protective devices crucial in hazardous acoustic environments. Different hearing protection devices are available, each tailored for specific applications. Here’s an analysis of the common types and their applications.
Earplugs
Earplugs serve as small inserts placed directly into the ear canal. This design creates a barrier against harmful noise levels, rendering them a practical choice in settings with persistent high noise levels. Disposable foam earplugs are favored for their cost-effectiveness and simplicity in use. Reusable versions, crafted from silicone or rubber, offer a longer-lasting solution. Custom-molded earplugs present the highest comfort level, crafted to match the individual contours of one's ear canal.
These devices provide effective noise reduction while being discreet and comfortable for extended periods. They prove instrumental in industries like construction or manufacturing, where unending exposure to loud machinery is prevalent.
Professionals emphasizing hygiene should consider banded earplugs. These feature a flexible band holding the plugs outside the ear canal when not in use, reducing contamination risk. The CDC offers guidance on selecting suitable earplugs. 3M E-A-R Push-Ins™ Earplugs are a great option for those looking for reusable earplug solutions.
Earmuffs
Earmuffs are equipped with soft cups to cover the entire outer ear, establishing an air-tight seal. Retained by a headband, they provide noise reduction across various frequencies and excel in environments with fluctuating noise levels. 3M PELTOR™ X Series Earmuffs are a reliable choice for noise reduction across different frequencies.
The principal advantage of earmuffs lies in ease of application, ensuring consistent protection without the need for ear canal insertion. This allows for quick deployment or removal where situational awareness may be required. Certain models incorporate electronic enhancements, such as integrated communication systems and noise-level dependent attenuation, enhancing utility in dynamic work settings. However, earmuffs might become cumbersome in extremely hot areas due to heat accumulation.
These devices are well suited to employment scenarios like aviation or military operations, characterized by sudden, extremely loud noises. In outdoor environments, earmuffs withstand environmental elements, offering durable protection for users.
Speak to an expert
Talk to our team about your safety or procurement needs. We’re here to help you find the right solution.
Contact UsCombination of Devices
In scenarios presenting exceptionally high noise levels, simultaneous use of earplugs and earmuffs can deliver superior protection. This dual device approach significantly enhances noise attenuation, an asset in environments where noise exposure exceeds regulated limits.
Selecting the correct hearing protector type crucially depends on the specific noise environment and compatibility with additional safety equipment. Investigating extra features, such as comfort and durability, increases the likelihood of consistent device usage.
For more comprehensive information on hearing protection options, resources like the CDC’s Noise and Hearing Loss Prevention page provide extensive knowledge on safeguarding against detrimental noise levels. By implementing tailored protective measures, safety professionals ensure reliable operational safety across various applications.
Understanding Hearing Protection Requirements
Ensuring employee safety involves understanding when hearing protection becomes essential. Exposure to excessive noise can lead to hearing impairment, making the comprehension of regulatory standards such as those from the Occupational Safety and Health Administration (OSHA) crucial. OSHA sets the permissible exposure limit at 90 decibels (dB) for an 8-hour shift. With each 5 dB increase, the safe exposure time reduces significantly; for instance, 95 dB necessitates protection after four hours, whereas 100 dB exposure permits only two hours without it. These guidelines aim to prevent noise-induced hearing loss, a common occupational hazard. Further details can be accessed through resources such as the National Institute for Occupational Safety & Health.
OSHA Requirements for Hearing Protection
Employers must heed OSHA's mandates for comprehensive hearing conservation programs if workers face average noise levels over 85 dB during the day. Compliance involves conducting regular noise monitoring, distributing appropriate hearing protection devices, and providing training on potential risks alongside preventive strategies. Annual evaluations, including hearing tests, ensure programs effectively adhere to the latest safety standards and cater to specific workplace conditions.
Situations Requiring Hearing Protection
Identifying scenarios where protection becomes necessary involves understanding environmental noise conditions. Construction sites, factories, and areas with heavy machinery or recurring loud noises often exceed safe levels. A simple rule: if normal conversation cannot be heard at arm’s-length distance, the area likely requires hearing protection. Employers play a key role in maintaining compliance through noticeable signage and regular noise assessments, promoting a proactive stance in preventing auditory damage.
Identifying the Need for Hearing Protection
Assessing the need for hearing protection depends on personal experiences and formal evaluations. Experiencing discomfort, a ringing sensation, or difficulty engaging in regular conversation indicates potential noise hazards. For precise assessments, decibel meters quantify sound levels, while occupational health experts provide professional recommendations based on workplace-specific scenarios. Ensuring workplaces adhere to safety standards helps avoid permanent hearing damage.
Meeting Protective Standards
Aligning with and adhering to hearing protection standards shields individuals from occupational hearing loss. By upholding OSHA regulations, organizations ensure employee health and enhance their protection against auditory damage, impacting overall safety and productivity. Access to well-fitted, effective devices is crucial in maintaining a safe and healthy workplace.
Enhancing awareness through educational initiatives enables workers to understand the necessity of hearing protection devices. Keeping employees informed of guidelines and ensuring adherence to federal and industry standards forms part of an effective safety management strategy. This focus not only reduces liability risks but ensures a safer working environment. Educating workers fosters compliance and promotes long-term auditory wellness.