Summary
Find What You Need
Browse our range of Working At Heights to find the perfect solution for your needs.
Understanding Working at Height: Essential Safety Protocols
Comprehending the intricacies of working at height holds paramount importance for safety professionals across various industries. This discussion will explore what constitutes working heights, identifying key safety measures, and examining global standards that ensure employee safety. Delving into these details can help industry leaders develop robust safety protocols.
Defining Working at Height
The Occupational Safety and Health Administration (OSHA) in the United States characterizes working at height as any task or activity that occurs six feet or more above a lower level. OSHA mandates fall protection to mitigate associated risks, emphasizing strict adherence to safety protocols. However, different regions follow their own definitions and regulations.
In the United Kingdom, the Health and Safety Executive views work at height as encompassing any scenario where a fall could lead to injury. They focus less on specific vertical distances and more on assessing potential hazards and consequences. Different interpretations underline the necessity of knowing region-specific standards when planning work above ground.
Height-Specific Safety Concerns
Industries implement specialized protocols to protect personnel working across various height levels.
Low Heights (Below 6 feet): Activities like standing on stools or short ladders may appear less dangerous, but caution remains essential. Rapid attention to detail can prevent accidents, ensuring even seemingly minor tasks maintain safety compliance.
Intermediate Heights (6 to 10 feet): Stronger preventive steps include guardrails and personal fall arrest systems. Employers play a vital role by ensuring that all installations effectively prevent injuries.
High Levels (Above 10 feet): Construction and industrial work conducted at these elevations demand detailed safety planning. Comprehensive fall protection, including harnesses and safety nets, becomes obligatory for workers exposed to greater risks.
Implementing Safety Measures
Work above ground level requires critical attention to established safety systems. Risk assessments identify potential hazards and foster the development of suitable safety measures. Employers bear the responsibility of executing these measures efficiently.
Fall Protection Systems: Key components such as harnesses, guardrails, and safety nets prevent serious injuries during incidents. Proper installation and regular checks reinforce the reliability of these systems.
Safety Training: Comprehensive training for workers on equipment use and emergency procedures boosts compliance with safety standards. Employers should conduct periodic refresher sessions to ensure that employees stay well-versed in the latest techniques and updates.
Regular Inspections and Maintenance: Conduct routine inspections of equipment and related systems to ensure their operational effectiveness. Professional inspections help avoid hazards linked to equipment failure.
Global Height Standards and Interpretations
Regional variations in height classifications reflect differing safety priorities. While OSHA remains a central figure in the U.S., other nations have their specific guidelines and regulations for work conducted at height.
The UK's Work at Height Regulations 2005 mandate a precautionary approach that views all elevated tasks as carrying risks, regardless of their height. This ensures a comprehensive evaluation of all relevant safety concerns.
In Australia, the approach involves broadly defining height-related activities, emphasizing the application of enhanced safety protocols for any tasks above ground. Other European nations integrate heights within their general workplace safety regulations, opting for an inclusive approach to falls risk management.
Meticulous considerations when organizing activities above ground are not only legal obligations but critical to fostering safer work environments. By taking into account the nuances of global provisions and implementing locally tailored strategies, industries can prioritize safety efficiently. Employers' proactive measures in risk management practices set the foundation for safer practices worldwide.
Recognized as industry leaders
Our awards highlight our commitment to innovation, quality, and delivering exceptional results.
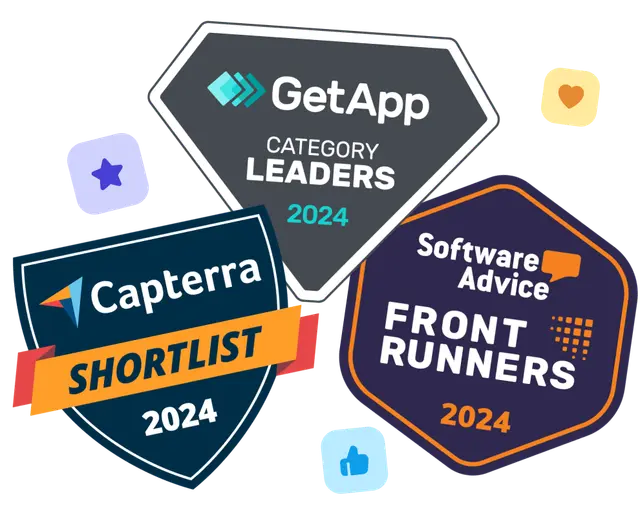
Fall Protection Requirements
Ensuring workplace safety involves comprehending fall protection systems essential for preventing accidents at job sites, particularly within construction and manufacturing sectors. The Occupational Safety and Health Administration (OSHA) defines specific guidelines that need strict adherence to maintain compliance and safeguard workers effectively.
Understanding Fall Protection Systems
Mechanisms designed for fall protection focus on securing individuals working at heights, with distinct systems needed for varying work environments. The major categories encompass guardrail systems, personal fall arrest systems, positioning devices, and safety nets. Each system serves a distinct purpose, with selection contingent on the unique requirements of each location.
Guardrail Systems: Barriers established at edges of elevated workspaces prevent falls. Commonly employed in construction and maintenance, guardrails offer a permanent passive solution for fall protection.
Personal Fall Arrest Systems: Comprised of a harness, anchorage, and a connecting device, these systems safely stop a fall in progress, thereby mitigating injury risks.
Positioning Device Systems: These devices support personnel working on elevated vertical surfaces, enabling hands-free operation.
Safety Nets: Placed below elevated work areas, nets capture falling individuals or equipment, preventing contact with the ground.
When Fall Protection Is Required
OSHA mandates fall protection for workers operating above four feet in general industry and six feet in construction. Additional requirements call for protection at lower heights when equipment or operations below present dangers. Different scenarios necessitate tailored solutions, such as temporary guardrails on construction sites or permanent systems within warehouses. Tasks conducted near hazardous machinery necessitate diligent compliance with fall and edge protection standards.
Advancements in Safety Training
Implementing effective fall prevention systems necessitates comprehensive safety training for employees and supervisors. Training aids in understanding correct usage, installation, and maintenance of fall prevention equipment. Essential topics include system fundamentals, identification of potential fall hazards, and the inspection of personal protective equipment (PPE).
Training initiatives enhance awareness of emergency protocols in case of a fall. Additionally, they cultivate a culture that anticipates workplace hazards and champions proactive measures.
Equipment Maintenance and Inspection
Routine inspection of equipment is critical in fall prevention strategies. Safety outcomes depend on maintaining equipment integrity, assuring proper functionality:
Examination of harnesses and connecting devices before every use
Detection of wear or damage
Verification of anchorage points to confirm they fulfill load capacity requirements
Implementing rigorous protocols for periodic audits, repairs, or replacement of defective components ensures workplace safety remains intact.
Maximum Working Heights Without Fall Protection
The limits for safe operation without protective measures vary depending on regulations. In the United States, OSHA requires fall protection when working above designated thresholds. The CDC highlights the importance of consistently evaluating risk factors at workplaces, allowing appropriate adjustment of protective measures. Employers aim to exceed these minimum standards to ensure optimal safety.
Continuous Commitment to Safety
Understanding fall protection requirements involves grasping regulatory elements and details. Businesses must remain adaptable to changing standards and provide exhaustive training tailored to each task. Regular equipment inspection, alongside versatile fall protection techniques, fortifies both employee safety and operational efficiency. Proper execution significantly decreases workplace incidents, protecting industries reliant on elevated operations.`markdown
Safety Training and Compliance
Importance of Training for Workers
Effective safety training plays a vital role in ensuring employees receive adequate preparation for tasks. This process provides individuals with the knowledge needed to identify potential hazards, utilize equipment securely, and respond appropriately during emergencies. According to the Health and Safety Executive (HSE), proper instruction strives to safeguard against accidents and contributes to overall productivity. For elevated tasks, special attention to fall protection becomes vital.
Types of Safety Training Programs
To address diverse needs, companies implement tailored training programs, each with a unique focus.
General Safety Training: Covers essential safety measures and emergency procedures designed to minimize risks and enhance overall workplace security.
Equipment-Specific Training: Concentrates on the appropriate use of machinery, personal protective equipment (PPE), and tools to ensure proper handling.
Job-Specific Training: Tailored to industry-specific requirements, such as chemical handling or electrical safety, ensuring workers meet legal and safety standards.
Explore further training resources for working at heights by visiting the HSE - Work at Height site.
Compliance with Safety Standards
Ensuring adherence to safety regulations offers multiple benefits, such as reduced workplace fatalities and injuries. Both employers and employees must understand relevant legal requirements to foster a safe environment. Regulatory bodies like the Occupational Safety and Health Administration (OSHA) establish rigorous standards, guiding organizations in maintaining workplace safety.
Establishing and Adhering to Standards
Compliance involves multiple vital tasks.
Assessing Workplace Hazards: Systematically identifying and documenting potential risks, including regular updates.
Implementing Control Measures: Developing procedures and safety protocols to mitigate identified risks.
Conducting Regular Inspections: Ensuring ongoing compliance through routine audits and reviews.
Updating Training Programs: Regularly revising training sessions to reflect changes in legal requirements and incorporate the latest technology.
At What Height is Fall Protection Required?
Fall protection guidance in the workplace depends on specific industry regulations. According to OSHA, fall protection generally becomes mandatory when employees operate at elevations of four feet or more in general industry workplaces. Construction activities require protective measures at levels of six feet or higher. Adhering to these regulations ensures personnel safety while meeting HSE guidelines.
Training should emphasize these regulatory requirements while ensuring workers understand the necessity and implementation of fall protection systems.
Best Practices for Compliance
Successfully meeting safety standards involves several strategies.
Conduct frequent training sessions addressing current hazards and emerging risks, maintaining a proactive approach.
Maintain detailed records of compliance activities, audits, and incident reports, ensuring clear documentation and accountability.
Foster open communication regarding safety practices between management and personnel, promoting shared responsibility.
Encourage employee feedback to continuously improve the overall safety program, leveraging insights from those directly involved in operations.
By focusing on comprehensive training and adherence to established standards, workplaces can create safer environments, reducing risks and promoting long-term success. Ensuring compliance not only protects personnel but also enhances productivity and morale across all levels of an organization. Investing in safety measures is not merely a regulatory demand but a commitment to workforce well-being and organizational excellence.