Summary
Find What You Need
Browse our range of Working At Heights to find the perfect solution for your needs.
Understanding Working at Heights
Working at heights remains a key element of multiple professions, especially those involving construction, maintenance, telecommunications, and diverse industrial sectors. The Occupational Safety and Health Administration (OSHA) defines working at heights as any task where an individual might fall from a certain altitude, posing a potential risk for injury if preventive measures aren't implemented. Fall Protection - OSHA
Key Activities and Potential Risks
Activities tied to this subject often include tasks undertaken on ladders, scaffolds, roofs, or any elevated structures. These tasks inherently carry the risk of falling due to elevation, making safety precautions vital.
Minimum Height Thresholds
A common inquiry relates to the specific elevation that classifies under working at heights. For the general industry, OSHA determines that the standard commences at four feet. By contrast, construction sectors set the benchmark at six feet, while shipyards commence at five feet. These diverse specifications reflect guidelines tailored to unique environments and associated risks.
Essential Safety Protocols
Safety fundamentally involves implementing fall protection systems. Employers bear the responsibility of integrating sufficient safety components like guardrails, safety nets, and personal fall arrest systems. Alongside technical safeguards, strong training programs enrich the overall safety strategy.
Industrial Significance
Work conducted at heights comprises a substantial component of operational tasks across various industries. Growing awareness and stringent regulations have evolved to address risks, thereby promoting safer practices and minimizing accident occurrences. As technology and methods progress, guidelines evolve alongside them, ensuring ongoing adherence to best practices.
Diverse Challenges
Encountered challenges vary, influenced by distinct elements like weather conditions, equipment reliability, and human factors. Effectively managing these variables requires diligent and comprehensive safety strategy planning.
Comprehensive Training Requirements
Training stands at the forefront of safety protocols for those engaged in elevated work environments. Emphasizing potential hazard recognition, the critical role of personal protective equipment (PPE), and appropriate equipment management practices ensures worker safety and resilience.
Disciplined adherence to regulatory frameworks and embracing continuous updates are pivotal in maintaining safety standards when working at heights. This vigilance not only shields workspaces but also boosts operational proficiency. Fully understanding varied industrial requirements, potential hazards, and mitigation techniques significantly contributes to advancing occupational safety management.
Safety Measures for Working at Heights
Working at heights poses significant dangers that necessitate proper safety measures. A comprehensive strategy encompassing regulations, training, and suitable equipment ensures personnel well-being in industries like construction or maintenance.
Understanding Working Height
Understanding "working height" is crucial in assessing potential risks. Working height refers to the distance from a platform or working area to the ground. It involves various levels and surfaces that influence the risks associated with potential falls. This concept includes ladders, scaffolding, rooftops, and other elevated workspaces. The Health and Safety Executive emphasizes implementing safety measures to prevent falls. Accidents during elevated tasks remain a leading cause of workplace injuries and fatalities.
Regulations and Guidelines
To achieve uniform safety practices, industrial and governmental organizations establish standards and guidelines. The Occupational Safety and Health Administration (OSHA) mandates fall protection during tasks conducted at more than six feet in general industry settings. This demonstrates the importance of robust safety measures. Implementing regulations ensures that human lives remain safeguarded.
Essential Safety Equipment
Protection through critical equipment proves crucial when handling tasks at significant elevations:
Fall Arrest Systems: Comprising full-body harnesses and lifelines, fall arrest systems play essential roles in avoiding severe injuries by preventing falling incidents.
Guardrails and Safety Nets: Employing these solutions stops personnel from accessing hazardous edges and halts falls. Not always practical in every scenario, but effective nonetheless.
Ladders and Scaffolding: Proper setup reduces unnecessary risks faced when accessing elevated areas. Regular inspections maintain the equipment in optimal condition.
Personal Protective Equipment (PPE): Helmets, gloves, and non-slip footwear provide an additional defense against hazards, acting as the final line of protection.
Recognized as industry leaders
Our awards highlight our commitment to innovation, quality, and delivering exceptional results.
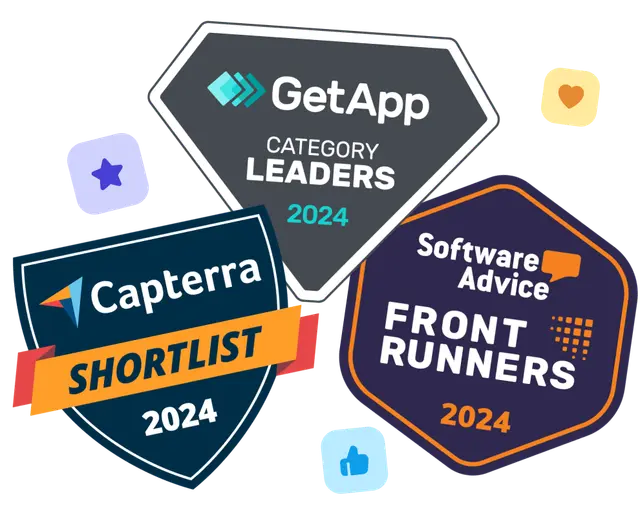
Training and Awareness
Continuous education, along with skill development, prepares workers to handle risk-laden environments successfully. Well-conducted training programs should encompass equipment use, comprehension of safety protocols, and situational awareness. Leadership must cultivate a safety-oriented culture that encourages vigilance and adherence to essential principles.
Risk Assessment and Hazard Control
Conducting regular risk evaluations remains crucial for identifying potential threats. Recognizing hazards before commencing operations enables the adoption of appropriate controls. Administrative measures like safety briefings and engineering solutions such as guardrails offer adaptability to varying work environments.
Fall Protection Systems
Thoughtfully integrated fall protection systems shield workers from grave harm. Considerate selection of fall protection equipment factoring in operational needs ensures a balance between mobility and security during elevated tasks.
Emphasizing Safety in Operations
Safety should be a core component of daily operations. Encouraging collaboration between management and employees contributes to a secure work environment. Leadership ensures that employees possess essential equipment, knowledge, and training to mitigate hazards effectively.
Industry guidelines stress a comprehensive approach to safe operations at height. The Health and Safety Executive's detailed overview of working at height offers valuable insights into these protocols. Prioritizing equipment, training, and awareness enables businesses to reduce risks associated with high-elevation tasks, protecting their most valuable asset: human lives.# Regulations and Compliance in Industry
Regulatory compliance stands as a cornerstone in bolstering safety measures within sectors such as construction and manufacturing. The U.S. Occupational Safety and Health Administration (OSHA) holds a critical role in driving these standards forward.
Speak to an expert
Talk to our team about your safety or procurement needs. We’re here to help you find the right solution.
Contact UsThe Role of OSHA in Safeguarding Work Environments
OSHA, founded to ensure workplace safety, delivers robust regulations that fortify worker protection. These encompass guidelines for fall protection, a pivotal element in safeguarding employees across diverse fields. OSHA mandates that employers furnish fall protection systems for tasks performed above specified heights, ensuring safety protocols are uniformly met. Comprehensive details regarding these mandates can be accessed on OSHA's official page OSHA Fall Protection.
The Necessity of Compliance
Meeting regulatory standards not only shields the workforce but also mitigates the threat of legal ramifications for employers. Complying with OSHA's safety directives is a legal requirement that notably curtails accident-induced expenses. Adoption of these measures cultivates a safety-oriented culture, indispensable within sectors rife with potential risks.
Sustaining Updated Safety Protocols
Achieving compliance demands businesses to persistently refine their safety procedures, aligning with OSHA's continually evolving regulations. Conducting regular audits and organizing training initiatives empower employers and employees with the knowledge to effectively apply these safety measures. Staying informed about regulatory updates is critical to maintaining a secure workspace.
Employing OSHA-prescribed protocols fosters environments where safety prevails. These standards, while introducing certain requirements, reassure reduced workplace mishaps and bolster workforce confidence in safety directives. Continuous emphasis on adherence supports not only compliance but also furthers the commitment to worker welfare and operational efficiency.
Ultimately, embedding compliance into daily operations strengthens industry practices, reassures employees, and promotes long-term success in safeguarding human resources—a vital asset across all industries.
Comprehensive Guide to Working at Height
What Constitutes Working at Height?
Engaging in tasks at a height introduces risks where falls can result in injury. This includes activities conducted on structures like ladders, scaffolding, or elevated platforms. Adherence to guidelines set forth by the Occupational Safety and Health Administration (OSHA) mitigates potential hazards by establishing clear regulations concerning these tasks.
Key Considerations for Working at Height
Professionals frequently need clarification on proper safety protocols when engaging in activities above ground level. The importance of using personal protective equipment (PPE), undertaking proper training, and adhering to legal requirements cannot be overstated. These factors form integral components of risk management strategies.
Questions Regarding Height Safety
Safety at height naturally attracts inquiries regarding equipment usage, risk assessment processes, and emergency rescue plans. Critical queries include: Is personal protective equipment like safety harnesses being utilized appropriately? Does regular inspection of safety gear occur? Are supervised workers well-versed in emergency response procedures? Such questions ensure preparedness for potential mishaps.
Addressing these concerns highlights the significance of best practices and regulatory compliance. Following OSHA's guidelines fosters a culture of safety by minimizing risks associated with elevated work environments. Convenient resources, such as online OSHA documentation, provide invaluable guidance, aiding organizations in establishing effective workplace safety programs. Emphasizing such measures cultivates environments that prioritize employee wellbeing.