Summary
Find What You Need
Browse our range of Bump Caps to find the perfect solution for your needs.
Understanding Bump Caps and Their Use
Safety professionals across diverse industries recognize the necessity of effective head protection. Bump caps, specifically designed for low-impact environments, serve as an essential layer of safety by protecting against minor bumps, scrapes, and minor head injuries. They are distinct from more robust options like hard hats.
Features of Bump Caps
Constructed from lightweight materials, bump caps typically feature an insert or pad, ensuring comfort for the wearer. Unlike traditional helmets, they prioritize comfort while maintaining protection. This balance makes them ideal for jobs requiring frequent navigation through low-clearance areas or around overhead obstructions.
Standard designs resemble baseball caps or baseball-style hats and include a reinforced insert. The unique design caters to professionals needing head protection without the burden typically associated with heavier protective headgear.
Appropriate Environments
Certain work environments benefit from bump caps. Warehouses, assembly lines, and similar settings commonly present scenarios where head bumps are likely. For professionals like auto repair experts, mechanics, and warehouse staff, these caps offer an optimal blend of safety and flexibility.
However, in settings with significant overhead hazards, bump caps should not replace hard hats. Understanding this distinction is crucial to ensure personnel receive the appropriate level of safeguarding.
Wearing Bump Caps on Site
Sites with minimal risks and low ceilings may permit the use of bump caps. While some construction sites may allow them under specific circumstances, exercising caution is vital. These protective items should be worn only after a thorough risk assessment confirms that the area does not necessitate the increased protection offered by hard hats. According to OSHA, employing the correct personal protective gear based on workspace safety requirements is essential.
Bump caps serve as effective head protection solutions in low-risk conditions. They offer comfort and security, making them an excellent choice for specific environments. Professionals should select their headwear based on the potential risk factors present in their workplace, ensuring optimal worksite safety.
Informed choices about head protection can significantly impact workplace safety. Bump caps and hard hats serve specific functions in safeguarding workers, and knowing the differences helps businesses preserve well-being.
Definition and Use
Bump caps represent lightweight safety helmets designed to guard against bumps and scrapes. These caps suit environments with minimal falling object risks, such as confined areas. Their design integrates a padded interior and a hard plastic exterior to counter minor impacts efficiently.
Conversely, hard hats serve as robust headgear to prevent injuries from severe impacts, penetrating objects, electrical hazards, and burns. Constructed from materials such as polyethylene or fiberglass, hard hats are indispensable across construction sites and any scenario with potential overhead hazards. Hard hats possess internal suspension systems and adjustable straps to guarantee a secure fit.
The CDC's National Institute for Occupational Safety and Health recognizes hard hats as necessary PPE in industries where overhead threats are present.
Regulatory Compliance
OSHA emphasizes distinct head safety requirements in occupational environments. Bump caps, classified under IMPA, fall short of OSHA criteria for sites with significant exposure to falling debris or high-impact threats. As a result, bump caps are seldom seen on construction sites necessitating compliance with OSHA's stringent safety mandates.
Hard hats must conform to the American National Standards Institute (ANSI) Z89.1-2014 standards, verifying their durability against substantial impacts and other hazards. In stark contrast to bump caps, hard hats meet the PPE requirements laid out by OSHA and are mandatory on numerous job sites, such as oil rigs, mines, and construction zones, where head injury risk runs high.
Protection Levels
The level of protection afforded by these headgear types varies depending on the work setting. Bump caps offer rudimentary protection against mild impacts, providing comfort while eschewing the mass of hard hats, thus making them ideal in low-risk environments like factories and warehouses. Nevertheless, they do not deliver the comprehensive defense necessary in more perilous locations.
On the other hand, hard hats deliver top-tier protection against significant head traumas, especially in industrial and construction sites with a looming threat of falling objects. Hard hats are designed to absorb energy from impacts, redistributing it to effectively prevent injuries.
Situational Use
Choosing between bump caps and hard hats hinges on specific work-related hazards. In environments like construction sites, hard hats are typically mandatory due to their durability and ability to handle unpredictable conditions. Conversely, for less perilous settings, where comfort and basic protection suffice, bump caps often emerge as the preferred option owing to their lightweight, breathable design.
Each type of headgear plays a vital role in workplace safety, and familiarity with their differences, along with regulatory prerequisites, ensures better injury prevention. Businesses must stay informed and provide the appropriate safety gear aligning with their operational requirements. Through education, workplaces can tailor their protective measures and thrive with a safety-first ethos.
Safety Standards and Guidelines in Head Protection
Ensuring adequate head protection is essential on construction sites. Mitigating risks from falling objects and impacts is crucial to creating a secure work environment. Familiarity with the relevant safety standards maintains this secure setting.
Prominent regulatory bodies, such as the Occupational Safety and Health Administration (OSHA), create strict benchmarks to safeguard employees. OSHA's directives on head protection are contained in Title 29 of the Code of Federal Regulations (CFR).
OSHA Regulations
The OSHA regulations specifically addressing head protection are found under 29 CFR 1910.135. These guidelines set forth requirements for the use of safety helmets, including when and how they must be worn. The headgear must resist penetration, absorb substantial shock, and sustain critical forces without damage.
Employers must confirm that head protection complies with the American National Standards Institute (ANSI) standards. Through rigorous testing, ANSI-certified equipment guarantees reliability in hazardous conditions. Adhering to OSHA’s requirements significantly reduces the likelihood of head injuries.
ANSI Standards
ANSI provides detailed specifications for the design and performance of safety helmets. The latest standard, ANSI Z89.1, encompasses aspects such as impact performance, penetration resistance, retention capabilities, and electrical insulation. Further, it classifies helmets into Type I and Type II, as well as Classes G, E, and C, according to their electrical insulation capacity and resistance to impacts.
FAQs: Bump Cap ANSI Approval
Bump caps serve a defined purpose but typically do not comply with ANSI certification for hard hats. Designed to shield against minor bumps instead of falling debris, these caps lack the thorough testing required for safety helmets. Consequently, bump caps do not offer the necessary level of protection governed by OSHA for construction sites.
Pay careful attention to manufacturer's specifications and warranty details to evaluate appropriate conditions for use. Although ANSI provides specific testing criteria, aligning product selection with the environment's demands and potential hazards remains vital.
Recognized as industry leaders
Our awards highlight our commitment to innovation, quality, and delivering exceptional results.
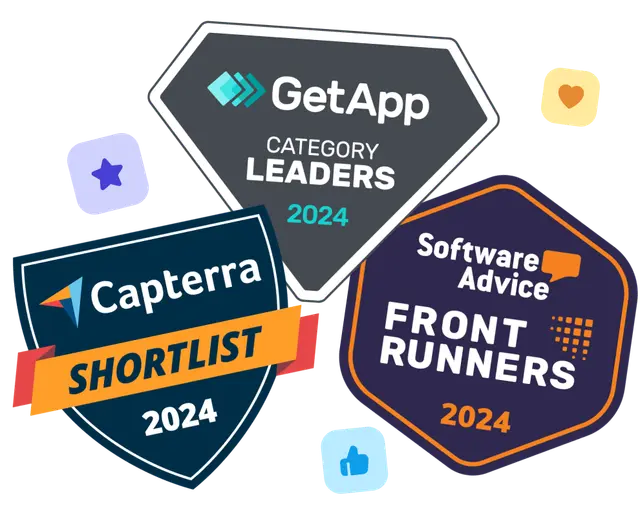
Key Safety Measures
Regularly inspect headgear to find and replace any damaged or deteriorated equipment.
Train employees on correct helmet usage and adjustment techniques.
Keep detailed records of compliance and adherence to equipment specifications for auditing purposes.
Following these standards, guidelines, and OSHA requirements not only ensures regulatory compliance but enhances workplace safety. This adherence fosters a culture of security and wellness at the job site. For in-depth information, refer to OSHA Regulations.
Frequently Asked Questions
Bump caps remain a prevalent topic in the construction sector, generating numerous common inquiries. Professional fields require clarity to maintain worker safety and prevent any misinformation.
Can bump caps be worn on-site?
Bump caps can indeed be utilized on-site, though one must assess task suitability. These caps offer protection for low-impact scenarios, such as accidental minor bumps or scrapes against stationary objects. Typically, in more hazardous environments, hard hats must be used due to their capacity to offer superior safeguards.
Is OSHA approval available for bump caps?
The Occupational Safety and Health Administration (OSHA) does not recognize bump caps as compliant head protection for environments where risks of falling objects persist. Mandatory OSHA regulations require employers to ensure employees use helmets designed to mitigate these hazards. More detailed standard information can be accessed through OSHA's official website.
Are bump caps classified as personal protective equipment (PPE)?
Bump caps belong to the category of personal protective equipment (PPE), providing defense against incidental contact. These caps serve situations that don't demand industrial-grade helmets, yet necessitate a basic level of head safety.
Do bump hard hats receive ANSI approval?
ANSI standards for industrial head protection do not cover bump caps as they lack the necessary structural integrity. In scenarios where more effective head protection is needed, full hard hats meeting ANSI criteria are indispensable.
Addressing frequently asked questions about bump caps contributes to a broader understanding among professionals in the construction industry. Recognizing when and where these protective aids are suitable informs safety compliance and enhances protection in a workplace.