Summary
Find What You Need
Browse our range of Workplace Safety to find the perfect solution for your needs.
Introduction to Workplace Safety
Workplace safety is a cornerstone of industrial settings, crucial for averting injuries, illnesses, and fatalities. Promoting safe practices ensures a productive, healthy environment for all stakeholders. Such safety measures extend beyond rule compliance, requiring active involvement from both management and the workforce .
Roles of Employees and Employers
Employers hold significant responsibility in formulating safety protocols tailored to their operations. Essential tasks include pinpointing and lessening hazards, providing adequate safety equipment, and ensuring well-structured training for their teams. Adherence to legal requirements, often encompassing routine inspections and meticulous record-keeping of safety incidents, is mandatory. Evolution of safety measures must match emerging risks for enhanced protection .
In contrast, employees bear a crucial role in supporting workplace safety. Participation in training programs and adherence to safety guidelines underpin their contribution . Active vigilance in identifying and communicating potential hazards fosters a joint safety effort. Continuous educational engagement allows workers to stay informed on current safety trends and procedures.
Importance of Training
Thorough training is an indispensable element of any robust workplace safety strategy. These educational initiatives impart vital knowledge to handle risks tied to designated roles. Training should address equipment management, emergency protocols, and proper use of protective gear . Consistent updates to training materials guarantee alignment with current safety norms, ensuring comprehensive risk management within the workplace.
Collaborative Efforts
Cultivating a safe workplace requires a united front, emphasizing both employer and employee dedication. Open dialogue facilitates timely updates to safety protocols, accommodating evolving threats. Establishing a culture where safety remains a priority reduces risks, bolstering workplace morale and efficiency.
Commitment to workplace safety not only mitigates accidents and litigation but also safeguards overall well-being, crucial for sustaining productivity and organizational growth. Exploring in-depth methods for hazard identification and management will yield valuable insights into a safe and effective work atmosphere .
Identifying and Eliminating Potential Workplace Hazards
Overview
A safe work environment hinges on identifying and eliminating potential hazards systematically. These processes play a crucial role in minimizing risks to personnel and assets. Organizations that employ well-structured safety strategies can foster conditions that protect employees and safeguard operations effectively.
Systematic Hazard Identification
A proactive stance involves conducting regular inspections and comprehensive assessments to detect threats within workspaces. Evaluations should cover equipment, procedures, and physical conditions at all operational levels. Using reliable methods such as job safety analysis and risk assessments is essential. Input from employees, who often have valuable on-ground insights, should also be encouraged. This participatory approach can enhance hazard management efforts significantly and ensure efficient implementation of safety measures.
Recognized as industry leaders
Our awards highlight our commitment to innovation, quality, and delivering exceptional results.
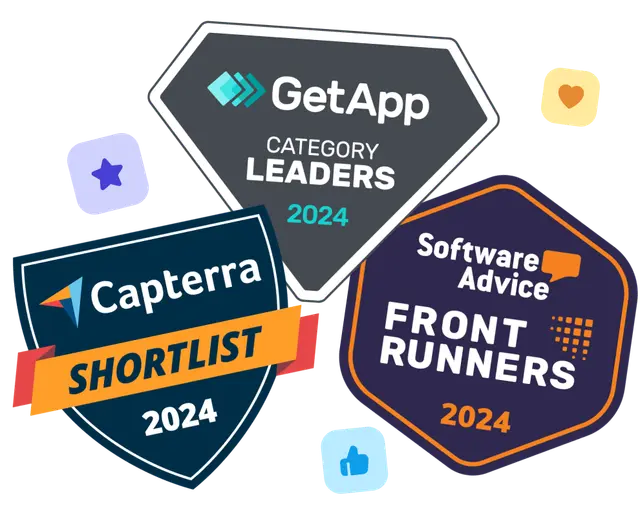
Communication on Hazards
Clear communication remains vital for effective hazard management. Ensuring workforce awareness about potential dangers and preventive measures is non-negotiable. Important tools in hazard communication include explicit signage, proper labeling of hazardous substances, and thorough documentation. Adhering to legislations such as OSHA's Hazard Communication Standard ensures information remains accessible and up-to-date.
The Importance of Good Housekeeping
Good housekeeping functions as a foundational aspect of safety in the workplace. It involves meticulous organization, cleanliness, and regular maintenance. Efficient disposal of materials and unused equipment prevents obstructions and potential hazards that may not be immediately apparent. Instituting robust cleanliness protocols ensures workplaces remain organized, reducing the likelihood of accidents significantly.
Strategies to Eliminate Potential Hazards
Employers should establish comprehensive safety programs to address potential hazards. Solutions include engineering controls, administrative policies, and personal protective equipment (PPE). Engineering controls often address equipment modifications or layout changes to minimize risk exposure. Administrative controls encompass training sessions and procedural guidelines that promote safe practices.
Fostering a culture of safety awareness involving employee participation contributes significantly to successful hazard management. Empowering workers to partake actively in safety initiatives can enhance these efforts. Institutions may consider incorporating an anonymous reporting system, which allows employees to report unnoticed hazards without fear of reprisal, further strengthening hazard identification processes.
By prioritizing systematic identification and elimination of potential hazards, organizations can substantially improve safety in the workplace. Engaging both management and employees in effective hazard communication, comprehensive housekeeping, and structured safety programs supports an environment where productivity thrives alongside security.
Training Employees on Safe Work Practices
Ensuring workplace safety remains paramount in any industry. Central to this effort lies consistent and comprehensive training, equipping employees with critical knowledge about safety protocols, precautions, and emergency procedures to mitigate risks effectively. Regular instruction serves as a bridge, connecting the workforce to new regulations, emerging hazards, and updated safety protocols.
Importance of Training Programs
Workplace training programs impart essential knowledge about safety procedures crucial for maintaining a safe environment. These initiatives aim to create an informed workforce capable of mitigating risks and responding smartly to workplace hazards. According to OSHA, businesses with effective safety programs can see reductions in injury costs, increased productivity, and enhanced employee morale. This development fosters a healthier work culture focused on safety and efficiency.
Key Elements of Effective Training
Understanding Safety Protocols: Comprehensive knowledge about safety protocols forms a foundation for cultivating a culture of safety. Protocols specific to job roles must be clearly defined, with regular updates integrated into training sessions to reflect industry advances.
Emergency Procedures: Effective training incorporates detailed emergency procedures, including evacuation plans and fire safety measures. Organizing mock drills plays a critical role in ensuring preparedness during real emergencies.
Safe Work Practices: Employees set to perform daily tasks safely should learn industry-standard safe work practices, encompassing both commonplace and unique safety challenges.
Role of Management in Training
Effective safety training relies heavily on management’s unwavering commitment. Leadership should prioritize safety by dedicating resources crucial for comprehensive training programs. Such a proactive approach not only assures compliance with safety regulations but also nurtures trust and transparency within the workforce.
Management Responsibilities:
Resource Allocation: Allocating necessary budget and resources for quality training sessions guarantees participants gain the best education on safety practices available.
Ongoing Education: Implementing ongoing education programs is essential to keep workers informed about evolving safety protocols and emerging threats.
Feedback Mechanism: Collecting feedback on training effectiveness assists in identifying gaps, refining programs, and better serving employee safety needs.
Additional Benefits of Safety Training
Comprehensive safety training programs yield benefits across the board. A well-informed team experiences decreased accident rates, paving the way for lower compensation costs and a more engaging work atmosphere. Furthermore, robust training boosts employee confidence in addressing safety concerns proactively.
Incorporating regular training into workplace safety initiatives demonstrates an organization's strong commitment to employee well-being, ultimately fostering a productive and secure environment. This dedication enhances operational efficiency and reinforces the overall integrity of the work culture.
Speak to an expert
Talk to our team about your safety or procurement needs. We’re here to help you find the right solution.
Contact UsEssential Workplace Safety Equipment
Workplace safety is paramount in diverse industry sectors. Employers who prioritize safety measures effectively demonstrate an unwavering commitment to worker protection. Implementing essential safety equipment remains fundamental to reducing on-site incidents and promoting a safer working environment.
Personal Protective Equipment (PPE)
Personal Protective Equipment, or PPE, provides an essential defense against workplace hazards. Helmets, safety gloves, goggles, and hearing protection are among the crucial components. Helmets protect against head trauma, particularly in construction and industrial settings. Gloves shield hands from cuts, abrasions, and chemical contact. Safety goggles safeguard eyes from debris, while hearing protection mitigates damage caused by loud noises, both critical in varying industries.
Barriers and Railings
Barriers and railings represent physical prevention strategies in industrial settings that manage workplace hazards effectively. These structures keep employees away from dangerous zones and moving machinery. By marking hazardous areas, barriers enhance visual safety cues. Railings in elevated workspaces prevent falls, increasing employee confidence while decreasing injury risk. Implementing these measures creates a clearly defined, safer work environment.
Importance of Wearing Masks
Masks play a vital role in protecting against air quality issues and airborne hazards. Respiratory protection shields workers from dust, fumes, and gases. Industries like mining and welding emphasize the importance of wearing masks to prevent respiratory health problems. Implementing appropriate respirators in these environments directly impacts workers' long-term health and well-being.
Emergency Supplies
In any workplace, emergency supplies serve as key components in crisis response. Fire extinguishers, strategically placed, offer the first line of defense against fire outbreaks. First aid kits provide all necessary supplies for immediate medical assistance following injury, enhancing workplace preparedness. Eyewash stations are essential in industries dealing with chemicals, offering invaluable response when eye contamination occurs.
Selecting, implementing, and maintaining the right safety gear underscores an organization's dedication to fostering a secure work culture. Aligning with industry regulations and equipping personnel with appropriate protection reduces workplace accidents significantly. Providing essential training in equipment use empowers employees, ensuring the safeguarding of their health becomes an achievable priority.
Understanding OSHA Workplace Safety Guidelines
The Occupational Safety and Health Administration (OSHA) prescribes crucial workplace standards in the U.S., ensuring safe and healthy conditions for personnel across diverse sectors. Employers must comply with OSHA guidelines to mitigate hazards and elevate occupational health management. A comprehensive understanding of these regulations is vital for enterprises committed to compliance and employee welfare.
OSHA Safety Guidelines Overview
OSHA crafts guidelines across a spectrum of safety areas. These guidelines focus on several key components, including safe working environments, emergency procedures, and equipment maintenance. Companies must implement suitable measures catering to specific industry requisites, providing workers with optimal operational conditions.
Work Environment: OSHA requires workplaces to prevent incidents and avert dangers. Employers must confirm structural soundness, ensure proper lighting and ventilation, and remove obstacles that hinder workflow or pose risks.
Emergency Protocols: Cultivating robust emergency protocols bolsters confidence in workplace safety. OSHA mandates routine drills and thorough worker briefings on escape routes and assembly points.
Equipment Safety: Proper machinery upkeep and routine inspections are crucial. Employers must establish protocols to manage malfunctioning equipment, protecting the workforce from harm. OSHA insists on detailed records of inspections and repairs for compliance tracking purposes.
Workplace Safety Practices
Implementing effective practices diminishes risks innate to varied work settings. Employers should consider the following:
Conduct Regular Risk Assessments: Identifying potential danger zones and proactively resolving issues is imperative for maintaining OSHA standards and boosting safety.
Training Programs: Extensive education on safely handling tasks, correctly using protective gear, and adhering to operational protocols is crucial.
OSHA Rules and Compliance
For employers aiming to cultivate a compliant workspace, understanding OSHA regulations is essential. Businesses must actively monitor regulatory developments, adjusting practices to align with federal criteria.
Inspection protocols, comprehensive documentation systems, and transparent communication foster a culture prioritizing safety. Noncompliance with OSHA rules can result in substantial penalties, legal repercussions, and a damaged reputation.
In-depth insights can be found at OSHA Worker Safety Guidelines.
Compliance not only safeguards health and safety but also nurtures a proactive, resilient workforce. Employees will be better prepared to tackle challenges inherent to occupational settings. Implementing these standards lays the groundwork for a secure and efficient working environment.
Frequently Asked Questions About Workplace Safety
A paramount resource for worker protection, the Occupational Safety and Health Administration (OSHA), establishes guidelines that help businesses maintain secure environments. Below are crucial elements of their recommendations.
What are the 7 General Guidelines for Workplace Safety as Recommended by OSHA?
Train Employees: Regular training sessions equip staff with knowledge to ensure safety awareness.
Use Protective Gear: Employers must provide personal protective equipment (PPE) where necessary to safeguard individuals.
Report Unsafe Conditions: Workers are encouraged to report potential hazards without fear of repercussions, fostering a proactive safety culture.
Obey Safety Procedures: Adhering to established protocols minimizes the risk of injury or incidents.
Maintain Equipment: Keeping tools and machinery in good condition is essential in preventing malfunctions and accidents.
Clean Workspaces: Ensuring neat and orderly work areas helps eliminate unnecessary risks.
Conduct Safety Drills: Routine drills prepare employees for efficiently navigating emergencies.
For further information, please refer to the OSHA's website.
What are 4 Essential Safety Precautions?
Use Correct Tools Properly: Selecting and applying the right tool for each task reduces injury risks significantly.
Regular Breaks: Frequent breaks are essential to combat fatigue and maintain alertness.
Clear Emergency Exits: Emergency exits must always be accessible; never allow obstructions.
Follow Ergonomic Practices: Proper ergonomic practices help prevent physical strain and associated injuries.
What are 10 Personal Safety Rules?
Stay alert and vigilant, always aware of your surroundings.
Carefully follow all provided safety instructions.
Consistently wear suitable safety gear appropriate for tasks.
Never compromise on personal protective equipment' usage.
Immediately report any detected hazards.
Familiarize yourself with emergency procedures.
Avoid shortcutting standard procedures or tasks.
Regularly ensure work areas remain tidy.
Use equipment responsibly and as instructed.
Actively engage in safety education and training.
What are the Safety Guidelines to Keep You Safe as You Work?
Fostering workplace safety is about cultivating secure working conditions:
Develop and implement comprehensive health and safety policies.
Monitor adherence to recognized workplace safety criteria diligently.
Encourage safety-centered communication to build a culture of awareness.
Regularly assess and adjust safety protocols in response to evolving needs, ensuring up-to-date practices.
Commitment to these guidelines empowers a safer work environment, reducing potential accidents significantly.
Understanding Workplace Safety Meetings
Workplace safety meetings play an essential role in nurturing secure environments across every industry. These structured gatherings serve as a critical platform for discussing potential hazards, reviewing safety protocols, and enhancing overall organizational health. Open lines of communication about pressing safety issues and preventive actions ensure that employees remain both informed and engaged in cultivating a safer working atmosphere.
These meetings underscore the importance of proactive safety measures and a culture of awareness. They form an integral component of any robust safety program. By bringing teams together, these meetings focus collectively on potential risks, showcasing the organization’s dedication to accident prevention. Engaging team members in candid discussions identifies not only immediate areas of concern but also paves the way for long-term safety solutions. Consistent safety meetings have the potential to significantly reduce work-related injuries, promoting a vigilant and responsible culture among team members.
The main objectives of such meetings include preventive education and the sharing of valuable insights and experiences from past incidents. Common discussion topics may cover proper equipment usage, response procedures in emergencies, and industry-specific safety protocols. This collaborative effort fuels employee engagement in the overarching safety program, fostering a sense of shared reliability. This empowerment motivates workers to assume ownership of their working environment’s safety.
Routine workplace safety gatherings maintain and enhance secure conditions. These discussions act as a cornerstone for the continual improvement of safety protocols, offering crucial education on important issues while promoting teamwork. Employees gain firsthand opportunities to address any concerns or notable hazards they encounter, reinforcing their role as key contributors to the organizational safety culture.
More information on safety meeting guidelines and organizational safety initiatives can be accessed through the Occupational Safety and Health Administration's resources.
Key Components of Safety Meetings
Workplace safety gatherings play an essential role in nurturing a solid safety culture and averting workplace incidents. By fostering communication and collaboration, these assemblies aim to address essential topics to minimize danger while enhancing work environments.
Core Safety Topics
Key subjects deserve attention in well-structured safety meetings. Regular reviews of organizational policies and emergency procedures help ensure comprehension among all employees regarding their roles during crises. Analyzing recent incidents or near-misses while identifying their causes offers valuable lessons, reducing future occurrence probabilities. Updates on new equipment or procedures further equip employees with critical information to respond aptly during emergencies.
Risk Management
Incorporating risk management as a critical component of safety meetings ensures effective accident prevention strategies. Identifying potential workplace hazards and evaluating their severity aids companies in implementing necessary corrective measures. Discussions around the hierarchy of control—comprising hazard elimination, substitution, engineering controls, administrative changes, and personal protective equipment—are vital for reducing danger levels.
Employee Engagement
Active employee involvement significantly contributes to the success of safety discussions. Encouraging team members to voice concerns, ask questions, and offer proactive ideas concerning workplace safety fosters ownership and responsibility. By nurturing this engagement, safety evolves into a shared priority rather than following a top-down directive.
Essential Questions for Safety Meetings
Thoughtfully designed questions enrich safety meetings by promoting introspection and discussion. Key questions might include:
Are there recent incidents or near-misses necessitating discussion?
What hazards require immediate attention?
What measures can enhance the safety of our work area?
Do upcoming tasks introduce potential risks, and how can these be mitigated?
These inquiries highlight areas requiring improvement while encouraging proactive safety management strategies.
Safety meetings enhance communication, encourage risk awareness, and involve all team members actively, reflecting their significant contribution to creating and maintaining a safe workplace environment. These sessions provide a robust foundation for effective risk management and ongoing safety practice improvements.
Promoting a Safety Culture Through Meetings
Creating a robust safety culture requires consistent effort. One powerful approach involves organizing regular safety meetings. These gatherings play a significant role in maintaining compliance and cultivating a secure work environment. By leveraging meetings effectively, organizations can promote awareness, understanding, and commitment to safe practices among team members.
Importance of Regular Safety Meetings
These meetings provide a vital platform for exploring various safety concerns and proactive measures. Discussions address specific risks present in the workplace, tailoring strategies to minimize potential hazards. Open dialogues empower employees to express any safety-related issues, fostering a transparent environment where everyone feels valued and respected.
Enhancing Workplace Safety and Compliance
Holding these meetings improves overall workplace safety levels. Emphasizing adherence to safety protocols encourages vigilance and reduces potential risks. Ensuring compliance with regulatory standards guarantees that workers are protected and aware of their responsibilities.
Encouraging Continuous Training
Incorporating training during these gatherings proves essential in reinforcing employees' knowledge and skills. Training programs can deepen understanding of safety procedures and develop the necessary abilities to tackle emergency scenarios. Offering continuous learning not only hones capabilities but also underscores the organization's commitment to safety for all.
Benefits of a Strong Safety Culture
Organizations investing in a strong safety culture reap numerous rewards. These include reduced accident rates, improved employee morale, and increased productivity. Prioritizing safety creates an environment where everyone strives to minimize risks. Focusing on workforce well-being fosters a positive atmosphere, with engaged employees actively contributing to the organization's success.
Regular safety meetings emerge as a dynamic tool for nurturing a safety-focused culture. Addressing specific concerns, promoting compliance, and offering training opportunities actively contribute to establishing a safer, more productive environment. Enhanced dialogue during these meetings ensures that every participant has the chance to develop greater trust and commitment to workplace safety.
Frequently Asked Questions About Safety Meetings
What is the Purpose of a Safety Meeting?
Safety meetings aim to nurture a culture of safety within an organization. These gatherings serve as platforms for staff to learn about potential hazards, regulatory updates, and essential procedures that minimize workplace risks. Such meetings ensure strict adherence to established standards and legal requirements.
What is the Main Intention of Safety Meetings?
Promoting a safe working environment stands as the principal goal of safety meetings. By identifying potential dangers and reviewing past incidents, employees gain the knowledge needed to recognize and reduce risks. Introducing new protocols aids in accident and injury prevention.
What Do You Say in a Safety Meeting?
Discussion topics often include updates on protocols, procedures for hazard reporting, and reviews of previous incidents or near misses. Discussions might also cover newly introduced equipment or technology, along with any changes in safety regulations.
What Are Good Questions to Ask at a Safety Meeting?
In what ways can our team elevate safety procedures?
Are there recent incidents providing learning opportunities?
What emerging risks have surfaced in our work environment?
Which protective measures can be instituted to address them?
These questions promote active involvement and continuous dialogue among employees, helping to identify issues and devise solutions before they escalate.
Ensuring Workplace Chemical Safety
A thorough comprehension of chemical safety measures significantly enhances operational efficiency and long-term employee protection across various industries. Implementing comprehensive protocols safeguards individuals from hazardous chemical exposure, mitigating health risks and minimizing environmental impact.
Principles Behind Chemical Safety
Controlling chemical safety within workplaces requires meticulous planning and compliant practices for safe handling, storage, and disposal to avoid accidental exposure or harm. Critical to this process is ensuring personnel understand risks linked with hazardous substances and equipping them with requisite skills and tools for emergency situations.
Pillars of Workplace Chemical Safety
Comprehensive Risk Assessment
Prior to introducing new chemicals, an exhaustive risk assessment is essential to identify potential dangers. This method aids organizations in selecting specific protective measures tailored to mitigate inherent risks of each substance. Regular reviews adapt assessments to evolving conditions, aligning safety protocols with any new threats.
Employee Training and Development
The foundation of effective chemical safety lies in thorough training programs. Employees must gain expertise in PPE usage, hazard communication, and comprehension of labeling systems. Conforming to OSHA's Hazard Communication Standard is crucial, ensuring that all personnel are well-informed and prepared to handle hazardous materials safely.
Optimized Storage and Labeling Systems
Minimizing exposure and potential reactions depends on efficient storage solutions. Chemicals should be organized based on their properties, stored in compatible containers, and kept away from incompatible substances. Proper labels enable quick identification, highlighting crucial hazards and enhancing workplace safety.
Responsible Waste Management
Process-driven chemical waste management lowers exposure levels and protects environmental resources. Employing an appropriate waste disposal plan is vital for maintaining a safe workplace atmosphere and preserving ecological integrity.
Creating Robust Chemical Safety Protocols
Establishing reliable protocols to tackle possible scenarios involving chemical exposure or spills plays a pivotal role. Safety data sheets (SDS) must be readily available, offering detailed insights into chemical properties, hazards, and remedial measures. Routine emergency drills familiarize employees with response strategies, ensuring readiness in adverse situations.
Conforming to Regulatory Standards
Adherence to regulatory frameworks, such as those mandated by OSHA, is crucial. Keeping abreast of regulatory shifts promotes consistency in applying chemical safety measures across operations. Organizations benefitting from these frameworks provide a secure and compliant environment, fostering trust among stakeholders.
Nurturing a Proactive Safety Culture
Cultivating a workplace culture centered around safety is indispensable. Open communication channels, focusing on near-miss reporting and encouragement of continual learning, lay the groundwork for safety as an integral component of organizational ethos. Specialized teams overseeing workplace safety contribute to a proactive stance in risk management, leading to higher levels of operational success.
Enhancing chemical safety in workplaces builds trust and security. Comprehensive strategies encompassing risk assessments, extensive training, structured storage solutions, waste management practices, and regulatory adherence underscore the pillars of occupational safety and long-term success.
Common Chemical Hazards in the Workplace
Chemical hazards pose significant risks in diverse workplace settings. They are associated with a range of industries including manufacturing, construction, and healthcare. The detrimental impacts of hazardous chemical exposure underline the necessity of understanding these risks for effective safety management.
Types of Chemical Hazards
Workplace chemical hazards fall into several categories, each presenting unique challenges. Awareness of these types aids in proper identification and handling:
Flammable Chemicals: Substances like acetone and gasoline can ignite easily and burn rapidly. Such hazards require stringent storage and handling procedures to prevent fire outbreaks.
Corrosive Substances: Chemicals such as sulfuric acid and sodium hydroxide have the potential to corrode surfaces and cause severe tissue damage upon contact. Facilities using corrosives need robust safety measures including specialized storage containers and PPE.
Toxic Substances: Certain chemicals, including arsenic and lead, affect bodily functions when inhaled or absorbed, possibly leading to severe poisoning or long-term health issues. Monitoring exposure levels and implementing safety protocols is crucial for safeguarding against these toxic agents.
Reactive Materials: Some materials, like bleach reacting with ammonia, can explode or produce hazardous by-products when mixed. Proper storage and handling guidelines mitigate risks associated with unintended reactions.
Irritants: Compounds such as ammonia and formaldehyde may irritate the respiratory system, skin, or eyes. Ventilation and protective gear reduce the adverse effects these chemicals may cause.
Comprehensive labeling and safe handling instructions help manage these risks, ensuring chemicals in the workplace remain stable and secure.
Potential Health Impacts
Chemicals present in work environments can lead to various health issues. Immediate exposure often results in symptoms such as dizziness, irritation, or headaches that may abate once exposure diminishes. However, prolonged exposure to harmful chemicals poses more severe threats, leading to chronic disorders including organ damage, respiratory ailments, or even cancer. Factors affecting severity include chemical nature, exposure magnitude, and individual vulnerability.
As highlighted by the National Institute for Occupational Safety and Health (NIOSH), recognizing and controlling chemical exposure aligns with prioritizing worker health. Additional information on safety practices can be gleaned from CDC's Chemical Safety.
Assessment and Management of Risks
Creating a safe work environment hinges on effectively assessing and managing chemical risks. Begin by evaluating an organization's chemical hazards, studying properties, exposure routes, and estimating exposure frequency and duration. Better assessment leads to more effective risk management strategies.
Training on recognizing and handling chemical hazards, combined with the use of personal protective equipment (PPE) like gloves and goggles, reduces exposure risks. Proper storage and ventilation, including fume hoods, further mitigate hazards.
Regulatory Standards and Guidance
OSHA's Hazard Communication Standards (HCS) establish comprehensive measures for managing chemical hazards. Compliance requires employers to classify chemical hazards and communicate relevant information to employees through Safety Data Sheets (SDS) and clear labeling. By following these standards, workplaces foster a structured chemical safety culture. Environmental Health and Safety (EHS) professionals play a vital role in ensuring adherence to these practices.
Tools for Identifying and Controlling Chemical Hazards
Accurate identification and control of chemical hazards are facilitated by various tools:
Safety Data Sheets (SDS): Provide meticulous details on chemical properties, potential hazards, handling, and emergency protocols.
Chemical Abstracts Service (CAS) Registry: Offers unique identifiers for chemical substances, aiding precise tracking and management of hazardous chemicals.
Gas Detection Systems: Crucial for monitoring air quality and real-time detection of toxic gases, enhancing workplace safety protocols.
Incorporating these tools into safety strategies enhances an organization's ability to manage chemical risks effectively, promoting a safe working environment for everyone involved.
Maintaining chemical safety in occupational settings demands thorough understanding and proactive management. Access to up-to-date information, compliance with regulatory standards, and deployment of cutting-edge tools ensures that worker safety remains a top priority. Consult resources from institutions like NIOSH and OSHA for further guidance on chemical risk management.
---
Handling chemicals is a crucial operation within many industries. Proper management safeguards both employees and the environment from harmful exposure. Prioritizing safety procedures reduces the risks associated with chemical handling and contributes to overall workplace safety.
Safe Handling Practices
Implementing comprehensive protocols can mitigate potential hazards. Begin with Proper Labeling and Storage. Ensuring chemicals are accurately labeled with clear hazard symbols and warnings prevents accidents. Utilize approved containers and ensure incompatible substances remain separated to avoid dangerous reactions.
Use of Personal Protective Equipment (PPE) proves critical in minimizing exposure to harmful substances. Adequate gear, including gloves, goggles, and respirators, must be provided to workers. Regular inspections keep PPE in optimal condition, and replacements should occur as necessary.
Comprehensive Training forms the foundation of chemical safety. Training programs should cover all necessary procedures, including understanding Safety Data Sheets (SDS), emergency response protocols, and efficient usage of spill containment kits. Employee education empowers staff to handle chemicals safely and confidently.
Ventilation Systems play a vital role in reducing inhalation risks. Effective air circulation helps control chemical concentrations in confined areas, further enhancing safety standards.
Frequent Regular Safety Inspections are essential in identifying potential hazards. Conducting audits ensures compliance with safety regulations and helps in early detection of issues. Addressing these promptly can prevent accidents and maintain a safer work environment.
Integrating these safe handling practices within business operations contributes to a robust safety culture, diminishing the likelihood of workplace incidents.
Workplace Safety Measures
Adhering to these practices aligns businesses with regulatory guidelines, such as those established by OSHA (Occupational Safety and Health Administration). Familiarity with these regulations plays a significant role in enhancing occupational safety standards within workplaces. Detailed regulatory information is accessible through outlets like OSHA's Chemical Hazards page.
Health Considerations
Workers exposed to harmful substances face potential short- and long-term health challenges. Enacting preventive strategies like regular health screenings aids in early detection, thereby facilitating timely interventions. Providing employees with comprehensive information on chemicals' potential health impacts encourages proactive measures to safeguard individual wellbeing.
Industries engaged in chemical handling bear an essential responsibility to foster stringent safety protocols robust enough to protect all involved. Promoting a safety-oriented culture can significantly mitigate the risks of chemical handling, preventing accidents and promoting health within the workforce.
---