Summary
Find What You Need
Browse our range of Fall Protection to find the perfect solution for your needs.
Working at height presents unique challenges in construction and other industries where falling poses significant risks. Alberta places a strong emphasis on fall protection as an integral part of its workplace safety regulations. Understanding the importance of these measures and how they fit into Alberta's safety framework allows organizations to protect their workforce effectively.
Falls rank among the leading causes of workplace incidents and injuries, making comprehensive strategies essential. Alberta's laws require employers to implement fall protection plans when workers operate at heights greater than three meters or any scenario presenting a potential fall hazard. To ensure compliance, specific procedures include guardrails, safety nets, and personal harness systems, tailored based on the work environment.
Training acts as a cornerstone in enabling workers to utilize safety measures effectively. Employers must provide adequate instruction commensurate with the tasks employees perform. This training covers proper equipment usage, hazard recognition, and rescue procedures that are vital for minimizing risks across diverse job sites. By investing in education, companies cultivate informed workers who can identify hazards proactively and utilize safety equipment efficiently.
In Alberta, companies embrace fall protection strategies as part of broader regulatory compliance measures. Consistent inspections and evaluations ensure equipment maintains functionality, greatly contributing to workplace safety. Regular assessments also allow organizations to address any deficiencies promptly, maintaining a culture of vigilance.
Alberta's dedication to fall protection underscores the province's commitment to fostering safer working environments. By adhering to established guidelines and prioritizing ongoing training, enterprises fulfill legal obligations and demonstrate a commitment to worker welfare. Alberta's safety culture thrives through the application of fall protection measures tailored to meet the dynamic needs of various industries.
Understanding Expiration Guidelines
Understanding fall protection equipment and training expiration serves as the backbone for maintaining workplace safety, especially in industries requiring work at considerable heights. This commitment involves routine evaluations and re-certifications to uphold stringent safety standards.
Does Fall Protection Have an Expiration Date?
Fall protection gear, in most cases, incorporates an expiration date as specified by the manufacturer. These timelines often depend on materials and environmental conditions encountered during use. The Alberta Government's Fall Protection Rules stress the importance of frequent inspection and replacement, adhering to recommendations from manufacturers. This practice remains vital for businesses leveraging such safety tools.
Equipment, including harnesses and lifelines, can deteriorate over time, diminishing their effectiveness. This underscores the necessity for meticulous maintenance. While some products clearly declare expiration dates, others might outline maximum usage periods based on different conditions. Both require careful consideration to prevent equipment failure during critical operations.
When Does Fall Protection Training Expire in Alberta?
In Alberta, fall protection training is typically valid for three years. Post this period, refresher courses ensure compliance with evolving safety standards and practices. Consistent re-certification ensures workers stay abreast of updated protocols, reflecting technological advancements and safety regulation modifications.
Training encompasses both practical skills and theoretical knowledge, introducing trainees to novel equipment and revised safety procedures. This ongoing education strengthens safety measures and substantially reduces worksite incidents.
How Often Must Fall Protection Equipment Be Re-Certified?
Re-certifying fall protection equipment mandates adherence to designated schedules and inspection guidelines. A qualified individual must regularly inspect equipment, guided by the manufacturer's instructions or local regulations. ISO standards might detail specific requirements aligned with regional needs.
Re-certification involves a thorough examination of equipment for signs of wear, stress, or damage that could compromise functionality. Typically, certain equipment necessitates annual re-certification, although other categories may demand different frequencies.
Frequent evaluations depend significantly on usage conditions. Improper use or exposure to demanding environments accelerates degradation, necessitating more regular checks and potential replacements. Safety officers ensure these evaluations are conducted timely, aligning with safety protocols specific to equipment types and usage contexts. Collaborating with suppliers, operators, and inspectors ensures all equipment passes stringent checks and remains safe for users. More guidelines are accessible through the Alberta Government's resources: Fall Protection Rules.
Importance of Compliance
Upholding the validity of fall protection equipment and training highlights a broader commitment to workplace safety on a logistical level. Compliance with expiration guidelines safeguards users while fostering an organizational culture centered on safety, minimizing liabilities and accidents.
Implementing thorough training and inspection schedules cements commitment to reliable fall protection measures, establishing a foundation for maximizing safety protocol adherence across industries. Attention to these specifics fortifies user trust, ensuring operatives feel secure with the provided safety equipment.
Ensuring Compliance: Best Practices for Fall Protection
Maintaining compliance in fall protection is essential to safeguard employees and adhere to regulatory requirements. Several strategies can significantly reduce risk and enhance overall safety.
Regular Inspections and Maintenance
Regular inspection and maintenance of safety equipment constitute the foundation of compliance. Regulatory bodies, such as OSHA, require inspections before each use, verifying that equipment remains in excellent condition. Tools that meet these standards preserve the integrity of safety measures and prevent equipment failure. Scheduled maintenance and repair activities further guarantee that gear continues to function correctly, minimizing potential hazards.
Employee Training Programs
Comprehensive employee training programs support a culture of safety. Such initiatives educate workers on proper equipment use and care, reducing accidental misuse. By familiarizing employees with updated guidelines and procedures, organizations drastically lower accident probabilities. Training is an effective means to achieve compliance, as well-trained personnel are better equipped to follow preventive measures.
Documentation and Record Keeping
Meticulous documentation and record-keeping bolster compliance efforts. Keeping logs of inspections, maintenance activities, and incidents assures that an organization can present evidence of adherence during audits and assessments. These records are invaluable during accident investigations, providing essential insights to prevent repeat occurrences.
Regular Updates to Procedures
Safety protocols must be adaptable. Procedures require regular updates reflecting new industry standards and technological advancements. By embracing a continual improvement mindset, organizations ensure that their practices align with best practices. This approach enhances workplace safety and ensures readiness for changing regulations.
Recognized as industry leaders
Our awards highlight our commitment to innovation, quality, and delivering exceptional results.
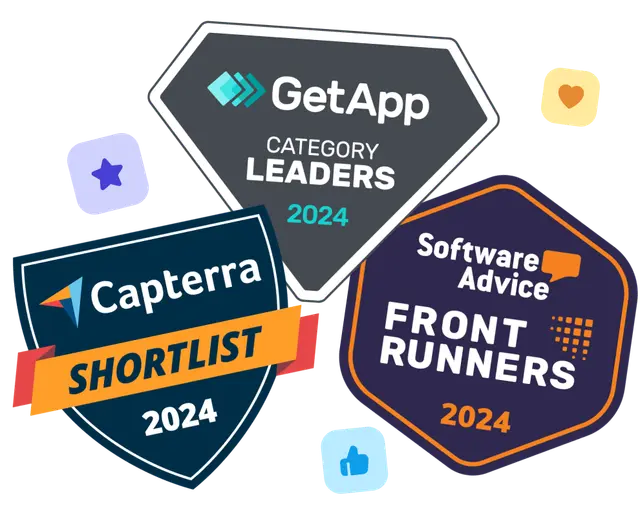
Usage of Personal Protective Equipment (PPE)
Promoting consistent use of Personal Protective Equipment (PPE) is crucial for safety and compliance. High-quality helmets, harnesses, and other gear must be utilized correctly and consistently. Proper PPE usage significantly reduces the risk of injury, demonstrating a commitment to safety standards and avoiding non-compliance penalties.
Developing Emergency Response Plans
Having a robust emergency response plan is indispensable. Quick, efficient responses during emergencies mitigate accidents' impact and ensure compliance. Regular drills and simulations prepare teams for real-world events, allowing immediate and appropriate action when necessary.
Clear Communication Channels
Clear communication channels strengthen fall protection measures. Workers need avenues to report hazards or incidents without fear of reprisals. By empowering employees to voice concerns about unsafe conditions, organizations foster a proactive safety culture. Open communication is essential to identifying risks early and addressing them promptly.
Implementing these best practices helps organizations maintain efficient fall protection measures. Compliance not only assures safety but also elevates industry reputation, demonstrating dedication to worker well-being.